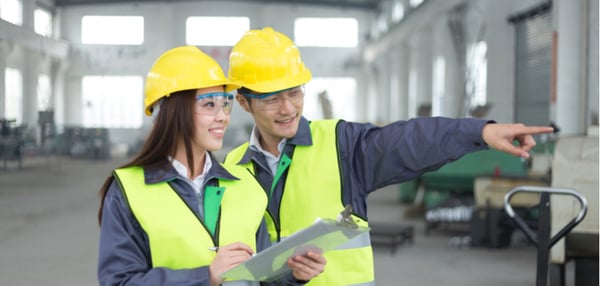
The idea of factory process improvement is something a lot of factory owners and managers in China are resistant to, but the truth is that improvement can be effectively managed and scaled up by simply starting out small.
Using “mini-projects” instead of wholesale factory shake-up is a great way to bring the team around to the idea that change can be good.
In this article, we’ll discuss how one can get started on the road to factory process improvement and how to scale it up to larger improvements.
Reasons For Resistance To Factory Process Improvement
One of the primary challenges for improving a factory or supply chain is the resistance of the factory managers to change.
They see the very idea that their factories or supply chain need improving as telling them that they are not good at their job.
Some leaders have just never seen a well-managed factory and do not understand how improvements can happen.
They are used to the industry they are in or the area they are in and see it as optimum as can be.
In many ways this makes sense.
The factory has made a lot of money in the past and they blame the downturn in profits on the government's new regulations or external factors from other countries, and not, perhaps, on their own inefficiencies.
Another factor, especially in purchasing and supply chain, is that people have made money through dishonesty and do not want someone to come in and expose them.
They are afraid of losing their secondary cash flow, or they are worried they may need to pay more taxes.
Regardless of the reason, this resistance to change prevents you as a customer or as a factory owner from making improvements that can ultimately help make you more money and generate more business.
Going Big Means Starting Small
Factory process improvement doesn’t need to intimidate, all it needs is to initiate change.
By picking one small area to change, a quick win can happen.
The key to quick wins with mini-projects is to get the team to pick an area they want to fix.
Everyone has an area they think can be fixed even if they are resistant in general.
Simple Steps To Follow In The First Two Weeks
- Select the area and give a 30-60-minute training on what the team wants to accomplish.
- Explain a basic principle of lean thinking that is related to the problem.
- Have the factory team work on it.
- Give them 2 hours to review the issue on the line.
- The next day give your team 2 hours to write down what they found.
- Reinforce the lean principle and add another one if needed with a quick training.
- On the third day give them some time to come up with a solution. Remember this is a very small problem to fix.
- On the 4th and 5th day allow the team to fix the problem and verify.
By actioning these steps you will give the factory team more confidence. The lean principles they learned will give them something to think about over the weekend.
The next week you can do this again and be more complex.
After two times, the team will be much more engaged in the improvement.
They will start to think of a larger project and often will find things you did not realize need to be improved.
Scaling Up For Bigger Improvements
At this point, the factory team is ready for a more in-depth class on lean manufacturing and quality improvement.
The classes should be set up to solve problems that are obvious, but will push the team to think.
This time, instead of a one week win, a longer mini-project can be taken on for 6-8 weeks.
This project should be more complex and may involve many areas in the factory. The team will likely still need guidance but will be more engaged and excited about the process.
Engaging the team in increasingly larger projects will save cost and improve quality as well as motivate them to look for new ways to improve.
They will start to push their management for more improvements.
People like to do well.
In fact, recognition and satisfaction in work is usually ranked above monetary compensation for what people want most from their job.
By doing these mini projects, you can move the team in a direction you want without creating fear or push back that would occur from rapid massive changes.
How has your team approached factory process improvement in the past?
What are some of the most important lean principles that you have taught/learned from in working through issues with your team?
Let me know in the comments section below...