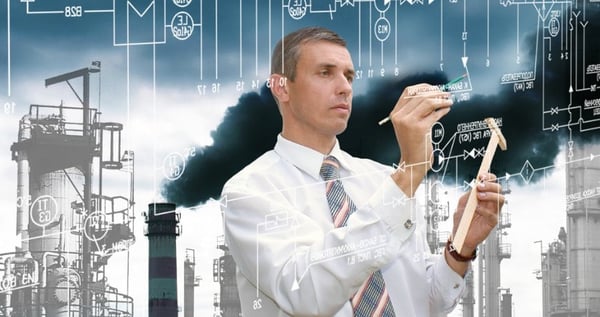
Industrial engineering has a bad image, dating back to Frederick Taylor. People think of the engineer who times operations and tells people “you should do this in 20 seconds or less, every time”.
Let’s say it clearly: 9 times out of 10, this approach doesn’t work in a Chinese factory.
Fortunately, there are many, many other industrial engineering applications that “work” and can drive positive business results in China manufacturing. In this article we’ll focus mainly on the objective of raising the productivity of factory operators by examining 7 Industrial Engineering applications in detail...
1. Industrial engineering for making materials “flow”
One central concept in modern industrial engineering is making materials “flow”. The less a product gets stacked somewhere, waits, is picked up again, goes through an indirect route, etc, the more efforts are wasted.
How to achieve that goal? Here are two pointers:
- Making the operations as compact as possible (typically, as a straight line or a U-cell) and keeping process steps as connected as possible;
- Balancing the lines so that each operator has about the same amount of work.
In other words, avoid “bottlenecks”.
2. Inventory reduction plan
One more thing that helps make China manufacturing operations more compact is to reduce inventory, and in particular work-in-process inventory (in other words, materials that are partly built/processed but not finished yet).
How to reduce inventory? It usually requires two types of changes:
- A production planning system that keeps batches just large enough – never making more products than current orders call for.
- Deep changes in procurement, and renegotiation of certain supplier agreements. The key is to order smaller batches. The unit price might go up, but it is generally easy to show that total costs go down.
3. Separating manufacturing work from internal logistics
A production operator should not have to leave his or her station, walk, pick up a new box, bring it close to the station, and so on. It is a big waste of time, as well as a distraction that breaks the focused attention they need to do their jobs well.
A small internal logistics team, sometimes operating as “water spiders” (going around quickly to fetch and replenish material) can save much time and decrease overall costs. There are expensive and complex software solutions to optimize material flow, but a good chunk of the benefits can be captured with a simple pencil & paper planning session.
4. Point-of-use presentation of materials and tools
For best results on point 3, materials need to be presented in an easy-to-reach fashion. The operator should only have to extend their arm to pick some material. To reduce fatigue and safety issues, pay attention to ergonomics – for example not having to lift a heavy object.
To make replenishment by internal logisticians easy, boxes of components are often placed on gravity-fed racks that are quite close to production workers. This is considered quite a “basic” industrial engineering application, and yet few Chinese factories have implemented it in their assembly operations...
If the components are relatively small, they can be presented this way:
Image courtesy of Assemblymag
Similarly, all tools that are used at least once a day should be available at point of use. It should be possible to grab them within a few seconds at most.
5. Having employees be part of writing work instructions
Training the staff is good, but doing so in a classroom setting is generally useless in China. A much better approach is to engage operators to be part of documenting the work instructions of their workstations.
They might not be able or willing to write them up, take nice photos, etc. but at the very least they should be consulted while the work instructions are being written/drawn. It increases dramatically the chance that they understand and adhere to those instructions!
6. Manufacturing automation
Automation is the hot topic these days. But journalists focus on what we’d call high-tech, full-automation projects. But there are many other shades of automation. A bit of semi-automation, such as automatic detection of a common mistake, or semi-automation of a process step so it takes 80% less time, can have a high impact on labor productivity without costing a lot of money.
When you are driving, you might not need a fully autonomous car. But it is nice to be able to set the car on “cruise” mode and keep it at, say, 120 km/h. On flat terrain, it will reduce the risk of speeding and over-consuming. Automation doesn’t have to be high-tech and leading edge!
From there, automate further in small steps. An improvement is an “adaptive cruise” feature that will reduce the number of times you hit the brakes and have to re-accelerate.
7. Never stopping
So you’d like to do a 3-month or a 6-month program consisting of applying industrial engineering tools in your factory? You might reach your objectives in that time frame, but the organization will regress to the previous state once management take their eyes off that ball.
Instead, you should develop a plan based on the opportunities for improvement, and update that plan on a regular schedule. It would include the number of days of work, the expected benefits, and related investment, if any.
There are many years’ worth of efficiency-improvement work in the average Chinese factory. It often makes sense to start in one area, then move to the next, etc. and to stage projects this way. Wages will keep increasing, so to counter that trend you need to keep investing in raising your productivity!
Have Your Say...
What do you think? Have you seen a factory improve its productivity very fast? Or, on the opposite, are you frustrated by the lack of improvement in your China manufacturing operations?
Let us know your thoughts, issues, and questions by leaving a comment below.