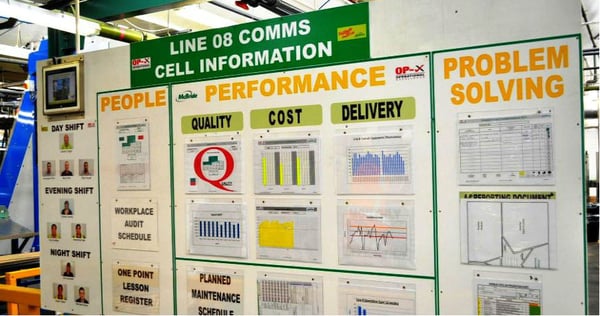
When a factory starts working on a lean initiative, one of the first steps involves putting up lean visual management boards on walls. We are not against visuals; nearly every project we do in the production area consists in putting up or improving on a board. But there can be common issues.
The Most Common Mistake You Can Make With Lean Visual Management Boards
If the factory has very mature systems and processes and has done quite a bit of training at all levels, there is nothing wrong with using lean boards. In other cases, those boards are not helpful.
"Unfortunately, they’re very often reduced to mainly redundant ‘window dressing’ that staff routinely ignore as they just don’t contain information that they find useful in their daily routines.” - Quality Inspection
And, since a lot of data posted are seen as useless (not to mention, they might be faked a few days before an auditor comes in), the staff becomes cynical about all posted information. It makes further improvement efforts harder. In some of the factories we visited, there is already enough decoration with all the ‘not for real’ work instructions!
4 Steps For a Successful Visual Management Board Set Up
- Step 1: clarify the company’s goals and objectives.
- Step 2: cascade those goals and objectives to each department, workshop, and team.
- Step 3: train the local leaders to “keep score” on a visual board.
- Step 4: use a mix of persuading and enforcing to get everybody to fill out their boards.
How Many Indicators Should A Lean Board Have?
It's important to remember that lean boards are for the users (who will fill them out with data and analysis) and their managers (who will read them, probe the local leaders, and push for improvements). Start with just one – for example, unplanned equipment downtime or first-pass yield. Get the local leader, or an operator, to report one key piece of information on a specific schedule.
And then make the most out of it – set a target, set plans to drive actions, and review the plan and the actions regularly. Once everybody sees the value of managing that one indicator, go for a second one. And so forth. Also, follow your needs – if the number one issue is productivity, track the number of pieces per labor hour (divided by the standard time, in case a line makes many different types of products).
Should You Include Sensitive Information On a Lean Visual Management Board?
Highly sensitive data (profit and loss, etc.) can be posted but kept in a locked room for management meetings only. Relatively sensitive data can be posted weekly, just before an appointment, and then taken out. For example, most factories consider HR data to be best kept away from governmental eyes. “Internal only” data can be removed when visitors come to the factory.
Lean Visual Management Board Examples
Make sure everybody in an area understands how the data is collected and what they mean.
Then, make sure they understand what is expected, as well as the current gap (expectation vs reality). And then comes the need for something seldom well done in China, the use of problem-solving tools. I listed the most common mistakes we see in an earlier article. This is not an area most Chinese managers excel at.
We see posters on the walls in maybe 90% of Chinese factories we visit.
- In Chinese-owned companies, it is usually exhortations for high quality, innovation, or whatever they think customers want to see.
- In Western-owned companies, they might proclaim how much they care about their staff, about safety, and so on.
You have good options for employee engagement, and slogans are not one of them.